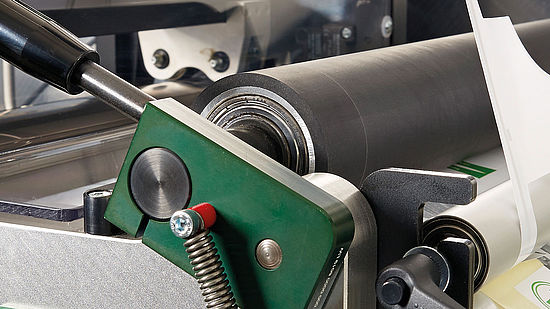
An effective aid for the fast and steady stripping of waste matrixes
Printing and processing machines are only as fast as the individual processing steps permit this and it is annoying if the expected production speed cannot be reached. For the production of adhesive labels the cause is often the stripping of the waste matrix.
Particularly for difficult cutting shapes with narrow sections in the label or broad gaps between the single labels the stripping becomes very often a brake for the production process. In order to reach nevertheless efficient speeds, customers use their own constructions or the material is pretreated accordingly. To reduce the release level, the surface material can be separated from the liner prior to the cutting and afterwards be brought together again. For materials with different expansion behaviours this additional step can sometimes result in wrinkling and air inclusions.
Particularly for difficult cutting shapes with narrow sections in the label or broad gaps between the single labels the stripping becomes very often a brake for the production process. In order to reach nevertheless efficient speeds, customers use their own constructions or the material is pretreated accordingly. To reduce the release level, the surface material can be separated from the liner prior to the cutting and afterwards be brought together again. For materials with different expansion behaviours this additional step can sometimes result in wrinkling and air inclusions.
The pre-cut material web moves directly into the LabelShifter, the liner is pulled downwards over a dispensing edge and deflected over an ajustable roller. The surface material with the cut label moves straight on and is transferred – without a fault in register - to a new position on the liner, freely adjustable in web direction. At the exit of the LabelShifter is a stripping unit which can be equipped with different rollers or a dispenser blade, the height is freely adjustable. In this way the angle for the stripping can be optimally adapted to the material and the waste matrix. The dispensing edge can also be exchanged depending on the material requisitions.
Aid for faster stripping
Der LabelShifter Plus ist an dieser Stelle ein wirkungsvoller Helfer, der selbst schwierigste Konturen mühelos bewältigt. Ursprünglich war der LabelShifter nur für das Versetzen von Etiketten konzipiert. Bei der Weiterentwicklung hat sich dann aber gezeigt, dass sich genau dieser Effekt positiv auswirkt, wenn direkt im Anschluss das Stanzgitter entfernt wir
At this point the LabelShifter Plus is an efficient auxiliary which can cope with even the most difficult outlines. Originally the LabelShifter was only designed for the shifting of labels. During the further development however it became clear that exactly this effect has a positive impact if the waste matrix is removed directly afterwards. The process is simple but effective:
The pre-cut material web moves directly into the LabelShifter, the liner is pulled downwards over a dispensing edge and deflected over an ajustable roller. The surface material with the cut label moves straight on and is transferred – without a fault in register - to a new position on the liner, freely adjustable in web direction. At the exit of the LabelShifter there is a stripping unit which can be equipped with different rollers or a dispenser blade, the height is freely adjustable. In this way the angle for the stripping can be optimally adapted to the material and the waste matrix. The dispensing edge can also be exchanged depending on the material requisitions.
The brief removal of the liner reduces the release value and due to the fact that the waste matrix is removed directly after this step, the process is clearly more effective. As the LabelShifter works absolutely reliably also at high speeds, even the removal of complicated waste matrixes is no longer a brake for the production process. On the contrary: the LabelShifter Plus can be easily integrated also in existing production processes and makes them far more efficient. Especially for counter-rotating outlines, thin materials with a high adhesive proportion and different label materials of paper or foil, the processing speed is mostly considerably increased.
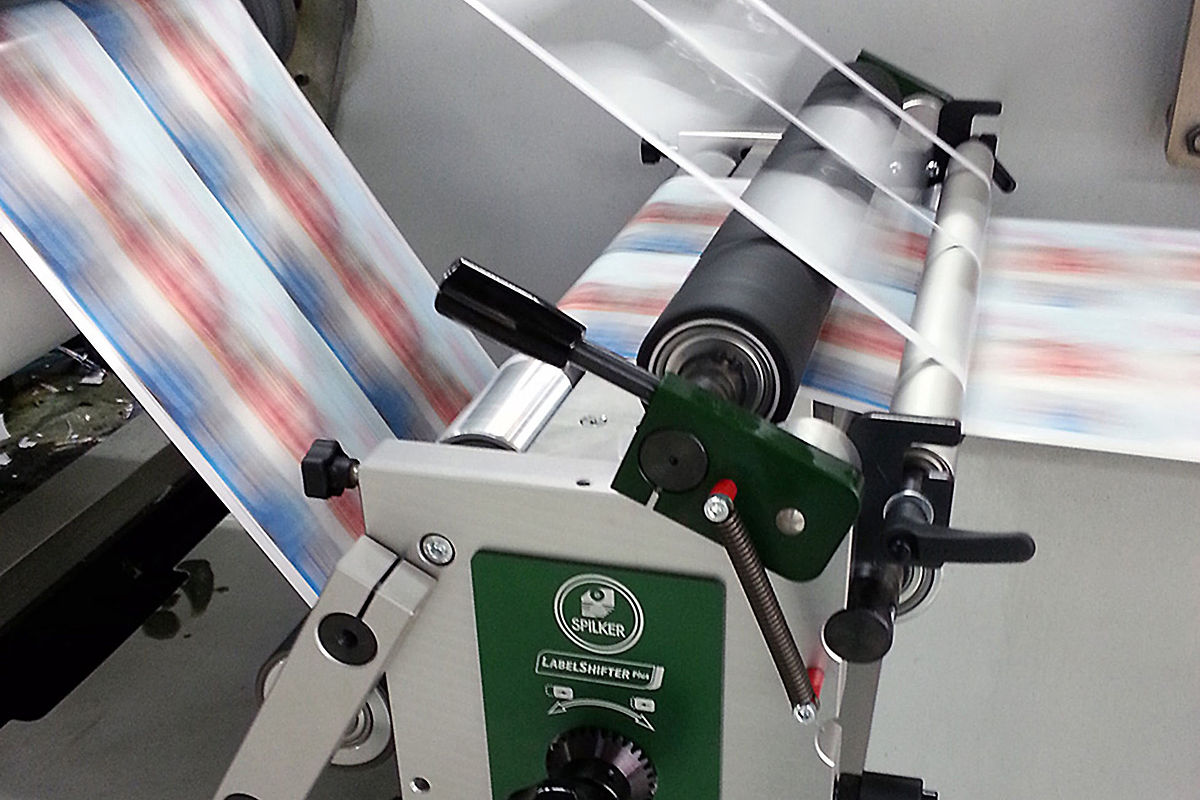
Company Conti-Label Pauwels NV is one of the leading producers of self-adhesive labels in Belgium and applies the LabelShifter for many orders. The modern machinery of company Conti-Label allows the use of different printing technologies in order to be able to produce all types of adhesive labels.
By the shifting of the labels with the LabelShifter it is ensured that there are no dispensing problems due to kiss cutting of the liner or bleeding of adhesives during the further processing.
"We have already been using the LabelShifter in our production for several years in order to offer our customers top quality”
states Bernhard Pauwels, General Manager of Conti-Label.
At a label producer in France, individual orders could only be processed very slowly due to complicated outlines. A recurrent order for labels with a difficult shape occupied one machine regularly during three complete shifts even though the material was heated prior to the cutting in order to improve the stripping. Since the LabelShifter has been built in this machine, the production runs significantly faster and the order is produced in less than two shifts.
Simple retrofitting in existing production processes
Narrow web machines and machines with a web width of up to 850 mm can be retrofitted with the LabelShifter. It is only important that there is sufficient space as close as possible behind the cutting station but before the traction unit and that the web guiding allows the installation.
For the fitting there are different options: a direct connection to the cutting unit or the installation in the machine. Depending on the type of machine, the LabelShifter is either mounted on a base plate or affixed on one side. Also the mounting at an angle of 90° and the installation in machines with a web run from right to left are no problem. No electrical connections and adjustments to the machine control are needed so that potential sources of problems do not even arise.
The LabelShifter is an uncomplicated and practical solution in order to optimise the production process. Companies who have already integrated the LabelShifter made by Spilker in their production are impressed by the positive impact on the total speed. The easy handling makes the LabelShifter Plus indispensable in the production already after a short time.
If you also require support with a project, you can find the right contact person here:
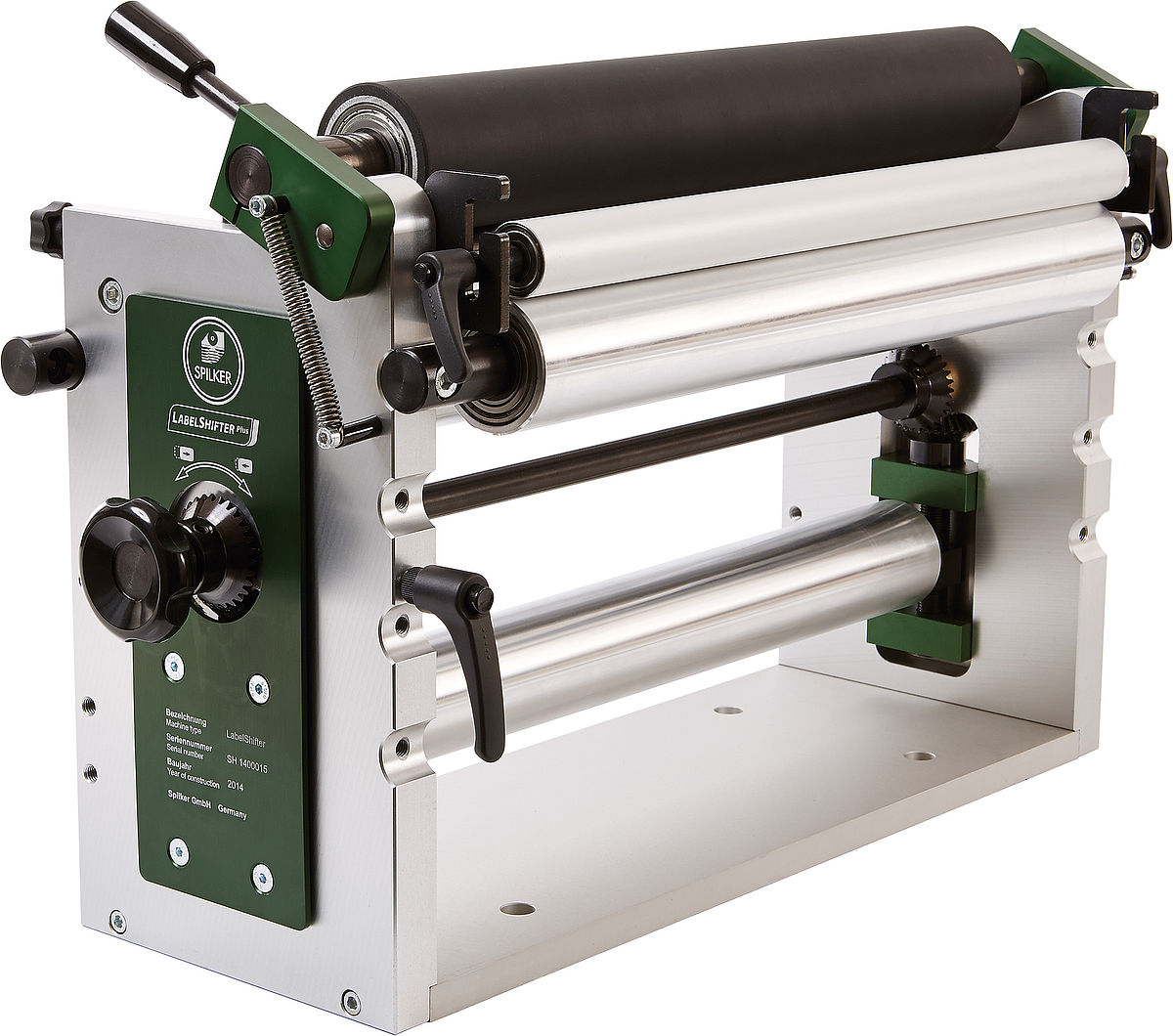