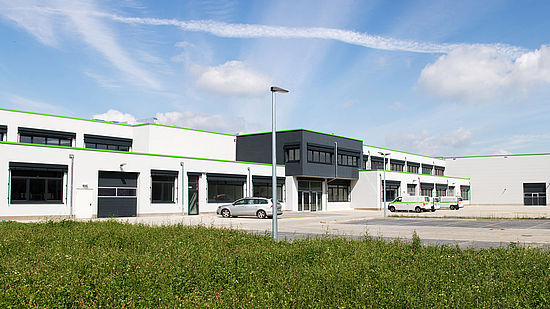
Newest standards in the flexible die production
After one and a half years of construction Spilker GmbH has completed its new location for the production of flexible dies in Lage / Kachtenhausen. On a surface of 3500 m² the latest production methods are used, which are unique in this form so far.
Since its founding in 1963 as a small engraving business, Spilker GmbH has grown into an established company and continues to thrive in the market today. The early specialisation in rotary tools ensured steady growth from the very beginning, which is why the company location and production in Leopoldshöhe have been steadily expanded to this day. Already in 1988, the production of flexible dies started there as a further mainstay and as one of the early flexible die manufacturers, Spilker has since then accompanied all technical developments on the market.
When the business area of the flexible die production was to be further expanded at the end of 2018, suitable building ground for a second site had to be sought. Because further expansion at the main site was no longer possible. The appropriate place was found in Kachtenhausen, only two kilometres away. This immediate proximity was important when choosing the location, because the synergies and many advantages of the short distances between the three company divisions of flexible die production, rotary tool production and the construction of special machines for the converting industry should certainly be preserved. After all, it is precisely this combination that enables Spilker to offer its customers comprehensive services far beyond the individual products.
For example, the main plant houses a technical centre with its own converting machines. Here, cutting tests can be carried out for customers under realistic conditions, own product developments can be tested and test setups and material tests are possible. The knowledge gained from all these tests and from the machine projects realised naturally benefits all areas of the company and thus also the flexible die production. Also at the main location there is an own construction and development department, which can realise individual adaptations and also offers suitable solutions for demanding requirements which deviate from the standard.
As the complete flexible die production is moving to the new location, urgently needed space will be available at the main site to further expand the production of rotary tools and mechanical engineering.
Production methods meet the highest ecological standards
Not only the building and building technology at the new location meet the latest energy efficiency standards, but the waste water treatment of the electroplating plant also meets the newest technical and ecological requirements. The modern water treatment plant purifies up to 15 m² of water from production every day and reaches drinking water standards. The environmental standard maintained is so high that it can subsequently be discharged directly into the city's sewage system. The residual heat from the production processes is collected in a hot water tank and used for cooling and heating the premises. The electricity generated by the 175 KWp solar plant is used directly in the production process, and any surplus is fed into the power supply system.
The use of state-of-the-art technology in all areas ensures greater precision in production, faster delivery times and an increased product quality. In this way Spilker guarantees short lead times and fast production times as well as maximum reliability through constant process monitoring.
„With the investment in the new site Spilker is further improving its product quality in the flexible die sector and is producing according to the latest technical and ecological requirements.“
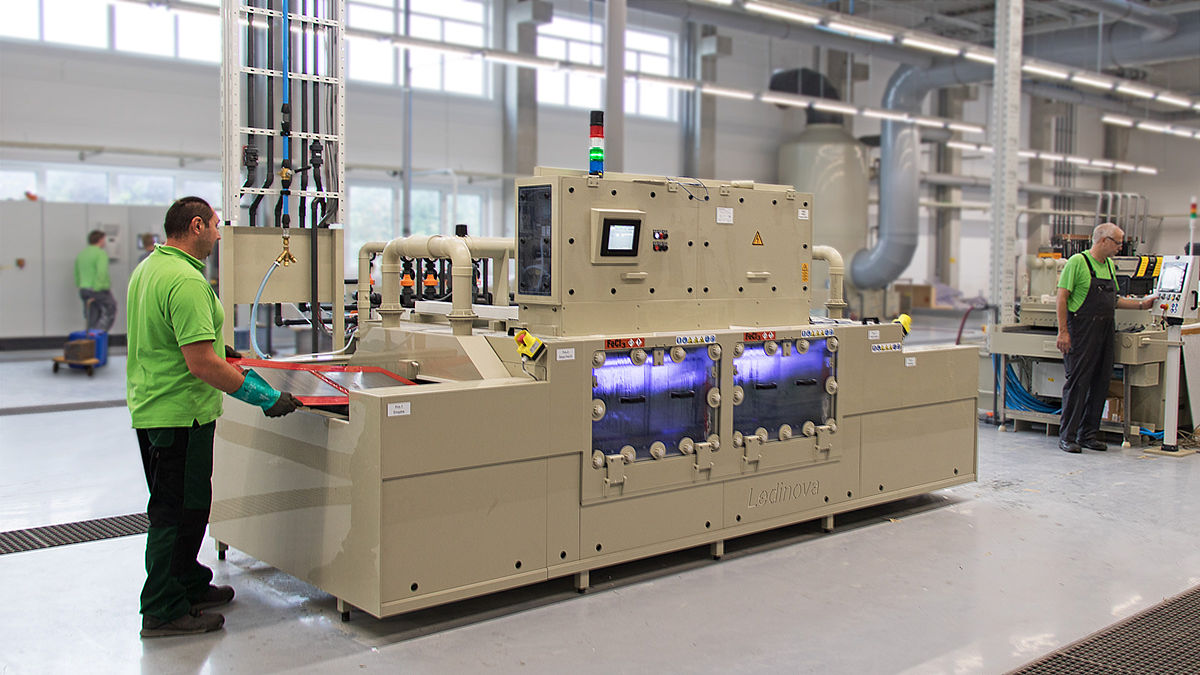
Also the production process was optimally organized. The individual manufacturing steps have been combined into production lines and the existing machinery has been expanded. The production around the clock makes it possible that flexible dies for which the order is received by 11 a.m. are delivered to the customer the very next day. In order to ensure this, the contour build-up and programming are carried out as soon as the order has been received by Spilker.
Depending on the required cutting height, the thickness of the base material is selected and the contour is printed directly onto the steel using large-format digital printers. In the next step, the unprinted areas are removed by a galvanic process. This corrosion process can be compared with accelerated rusting. The contour obtained is sharpened on CNC machines with the appropriate cutting angle. Afterwards each flexible die is nickel-plated. Nickel plating ensures optimum corrosion protection and is FDA compliant and approved for the food industry. In order to also speed up the ordering process, customers can send orders comfortably and directly to Spilker at any time via direct interfaces and the Spilker-Toolbar online ordering system.
Optional with non-stick coating and laser hardening
The flexible dies can be provided with various non-stick coatings, each suitable for special applications. All non-stick coatings are food safe and FDA compliant. Optionally, the flexible dies can also be laser hardened. In laser hardening, only the upper area of the cutting edge is specifically treated with heat, thus achieving extreme hardness. The required flexibility of the base plate is maintained. The laser hardening of the cutting edges increases the running performance and is therefore recommended for long runs, for cutting through and for film material that is difficult to cut.
During the final quality control, each die is checked for quality and functionality and a cutting test is carried out. The results are recorded in a test report. After approval by the quality control department, the flexible die is sent to the customer together with the test report and a sample of the die-cut.
This smooth production process, the daily practical experience, intensive cooperation with leading material suppliers and over 55 years of know-how make Spilker's flexible dies a top product. The production methods meet the highest ecological requirements, because sustainable environmental and climate protection are among the important corporate goals at Spilker. With the new location, the product quality of the flexible dies is increased, absolute reliability is guaranteed and faster delivery times can be achieved.
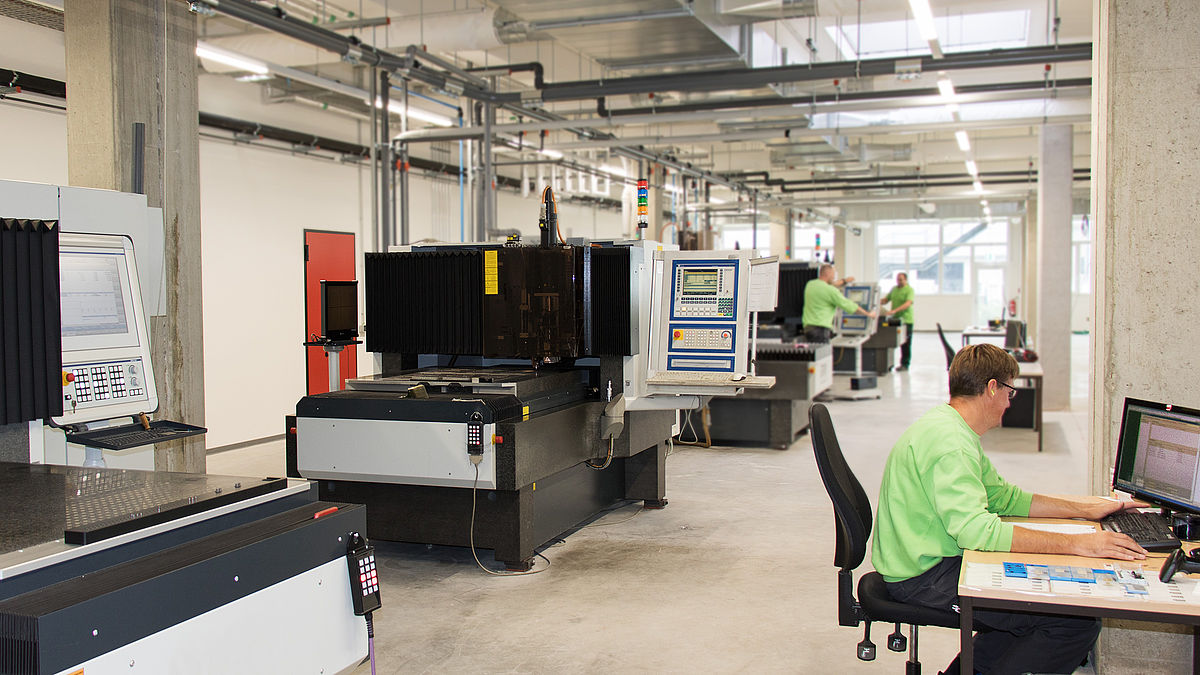