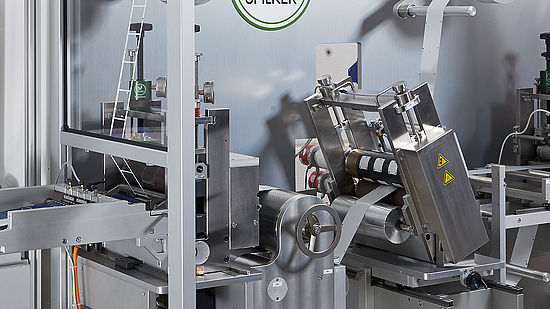
Rotary converting machines for medical and pharmaceutical products
The production of pharmaceuticals is subject to particularly strict regulations regarding hygiene, premises, equipment, documentation and supervision. Production takes place in cleanroom conditions, therefore the production facilities must meet the highest requirements.This is also valid for the recent development of the Spilker GmbH.
For the production of pain relief patches Spilker has designed a rotary machine which combines different dispensing, cutting and laminating processes with the final rotary heat sealing operation.
The processing of demanding compound materials requires absolute accuracy. An extremely precise cutting geometry and the absolutely exact cutting depth are essential specifically for cutting processes. Material combinations of foils, fabrics or metal foils combined with adhesives, active agents and the most different cover materials require a precision during processing as it can usually only be reached with rotary cutting.
Securing the product quality
For this machine project very different requirements concerning the production process, the handling and the securing of the product quality had to be met. And this began already with the development of the rotary machine. Also for this project the company‘ s own research and development department was an important component.
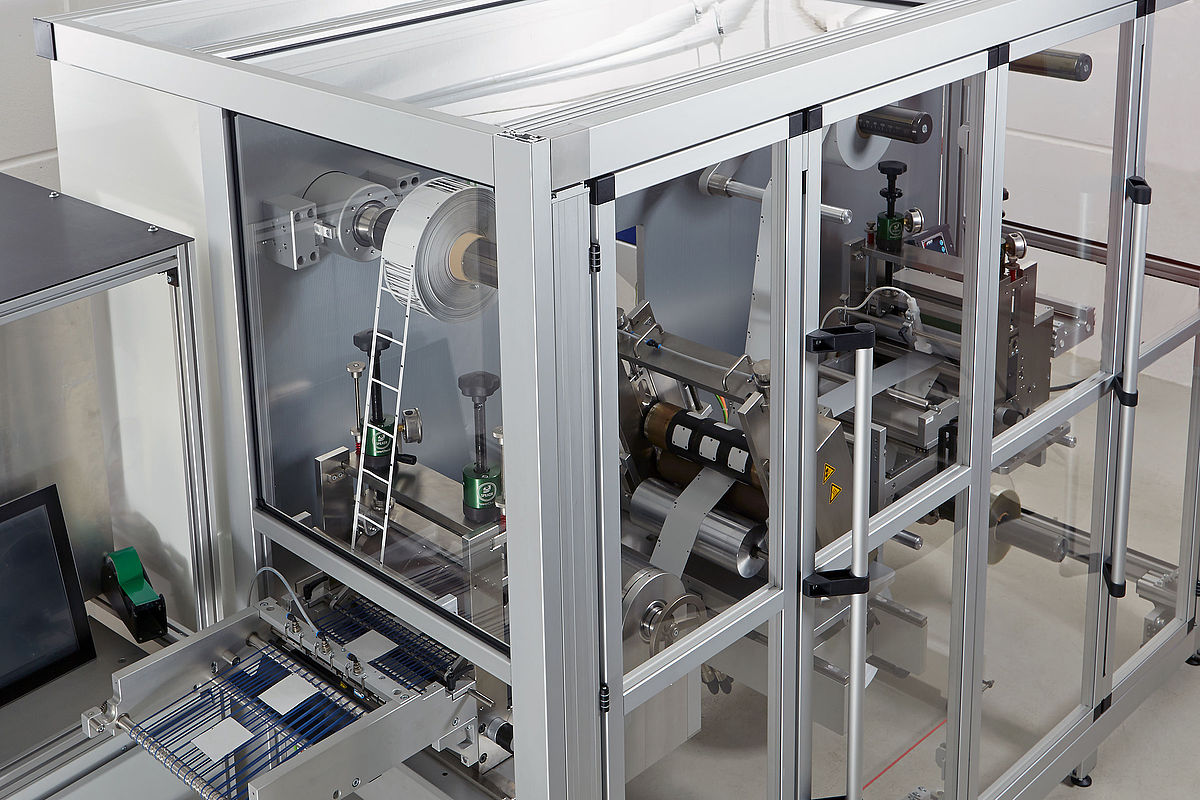
By means of 3D-CAD programs, the engineers created initial drafts and matched these with the individual requirements. Thanks to the extensive simulation functions the software permitted a real visualization of the project.
During the realisation of the project the customer is involved and can any time participate with his own suggestions. If necessary, prototypes and individual tools are produced and tested during the development stage. Thus Spilker makes sure that the further requirements for single processing steps are implemented.
In the assembly department the component parts produced in-house were fitted together. The programming and the initiation of all components were also carried out at Spilker. With internal test runs and the machine acceptance the actual development process was finalized. Numerous advantages result from the proximity of all production steps. The short distances between the individual areas facilitate fast communication which has a positive effect on the production speed.
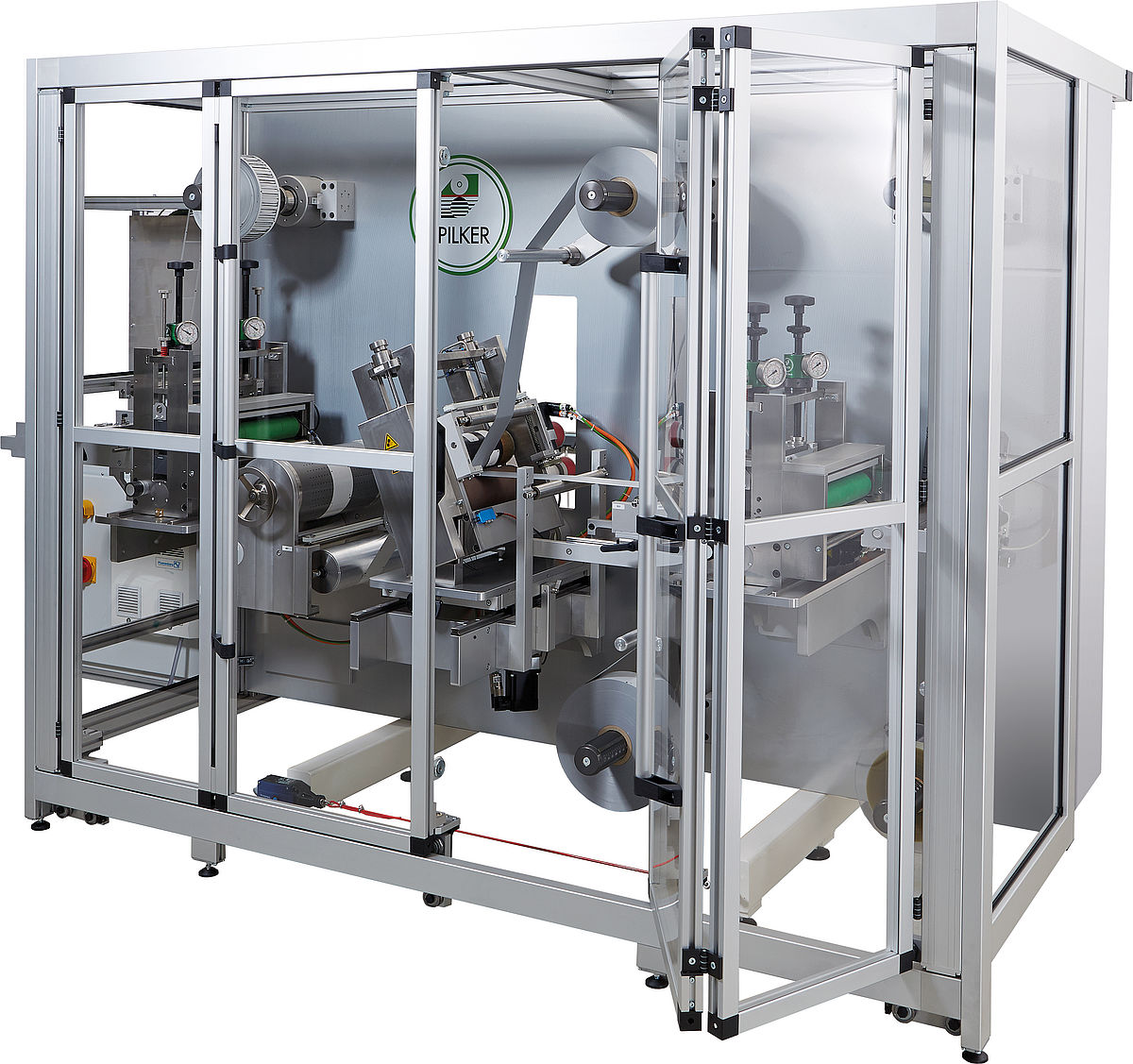
The departments are always in close contact, the production department can for instance give direct feedback to the development department, requests for modifications can be easily implemented. As a result also the customer will benefit from this who is involved during the design stage and the production phase and who will receive custom-made solutions. For the machine project servo technology is used for all drives. Operation takes place via a 24“ multitouch display with a user interface specifically developed by Spilker for this purpose.
Cutting-edge technology in use
Production speed is 30 metres per minute with a maximum web width of 300 mm, considering the high requirement profile of the product this is particularly fast and emphasizes very clearly the productivity. Due to the modular structure it is possible to integrate for example inspection and printing systems additionally or to add further processing steps.
With a length of 3,5 metres, a depth of one metre and a height of 1,8 metres the machine is surprisingly compact and also fits easily in narrow production environments and existing processes. The machine-made rotary tools comply with the high requirements of the pharmaceutical industry and can be provided with different food-safe coatings. For all tool and machine parts materials are used which ensure a maximum corrosion protection.
In order to guarantee additional hygiene and safety, the machine is surrounded by a protective cover of acrylic glass and anodised aluminium profiles. The cover can be opened on the complete length of the machine so that all machine sectors are easily accessible. Thanks to the acrylic glass the the interior space remains bright and perfect visibility of the machine is ensured.
Coming from a roll, the patch material is initially individualised, and a notch is cut to enable an easy opening of the single patches. By static charge the patches are afterwards held in exact position on the lower sealing material. The material web with the patches is hermetically sealed by heat with a second web of sealing material. The readily sealed patches are individualised in a further cutting process and are released on a delivery belt.
If you also need assistance with a project, you will find the right contact person here.
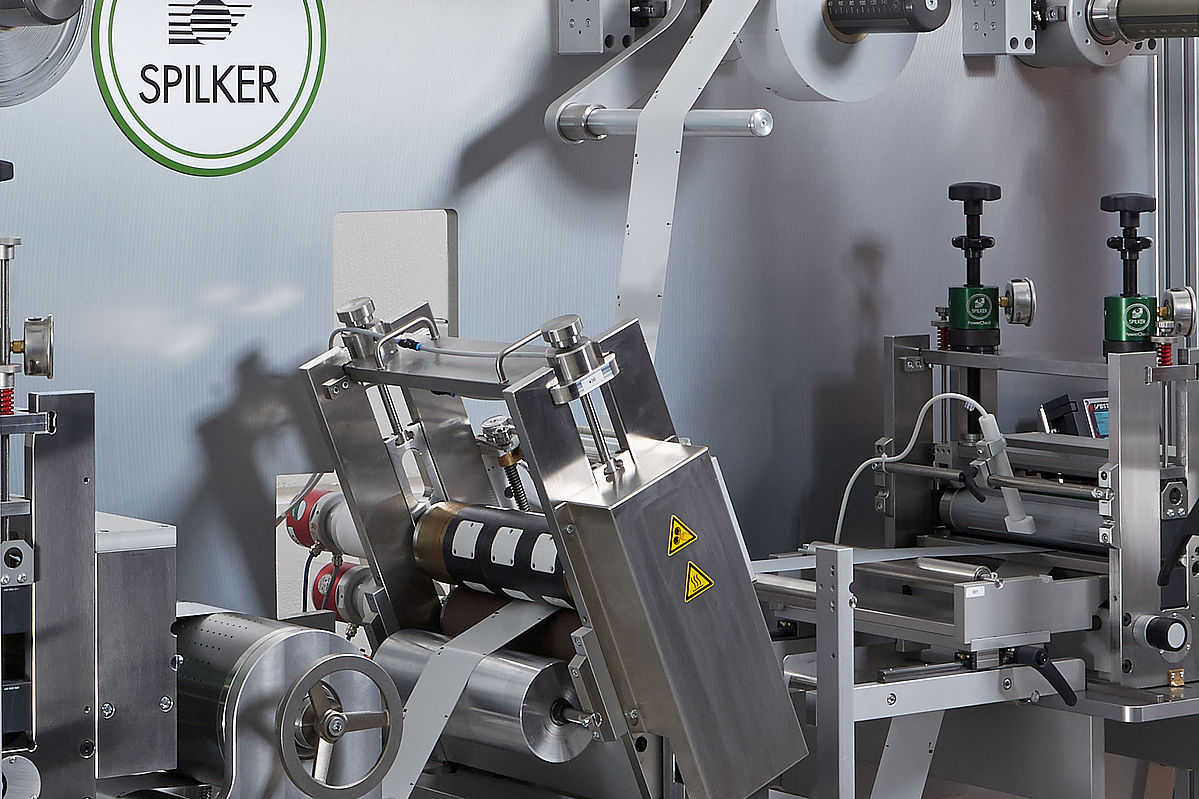