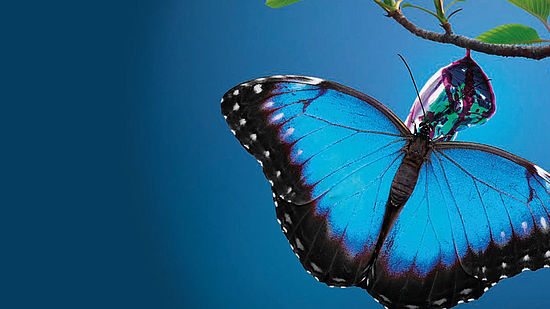
Efficient label production without liner
Use waste as a resource
The reduction of waste is one of the biggest economic and industrial challenges for the packaging industry. Increasingly, customers and brand owners are demanding sustainable production processes and the avoiding of waste due to the demands of end consumers, public institutions and politics.
Also in the production of self-adhesive labels these demands of the market for environmental protection are a challenge. New solutions are needed. Usually the printed label material is placed on a liner. The contour of the labels is cut with rotary cutting tools, the cutting edge of the cutting tool separating only the label material without damaging the liner. There are minimal distances between the individual labels. The result is a matrix, which is removed and ends up as waste. During the further processing the finished labels are then dispensed via a dispensing edge on the respective product, the liner is then also disposed of.
In order to use the otherwise wasted material appropriately and to significantly reduce the amount of waste produced, the material manufacturer Ritrama, after several years of research, has developed Core Linerless Solutions®: a technological platform based on a multifunctional liner that changes from waste into resource.
CLS: Core Linerless Solutions®
The process starts with Ritrama's self-adhesive CLS® Multifunction Smart Liner (Polypropylene with siliconized Polyester Liner, see graphic), which can be printed using all conventional printing techniques. The press can operate at full speed, because in contrast to inline converting, where the labels are already cut in the machine, no cutting process and matrix removal slows down the machine. The CLS® material is available in transparent, white and silver and with a thickness of 42 μm significantly thinner than conventional foil material.
After printing, in a lamination module by Omet, the siliconized liner is separated from the face, the thermal activable adhesive is activated by heat, and the liner is laminated to the printed material side. In this way, the liner becomes an integral part of the label and protects the printed image.
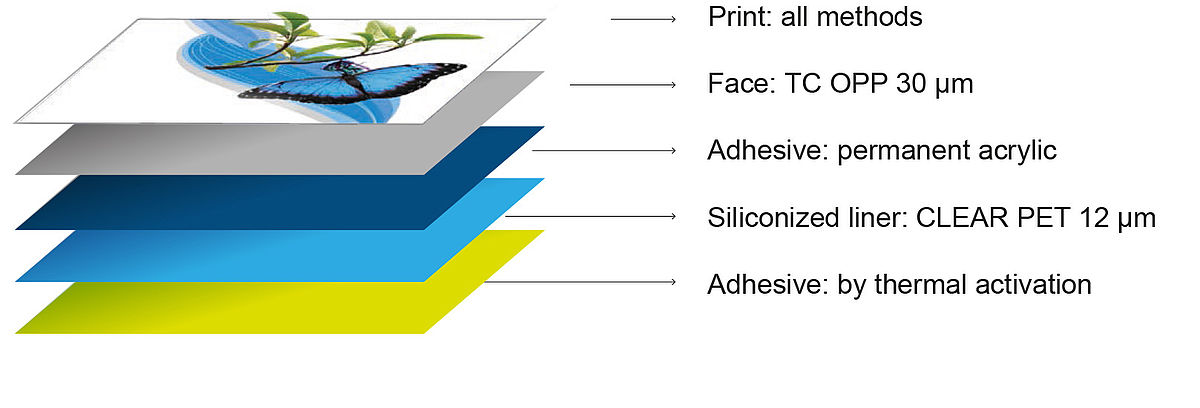
Converting Process
The finished labels are finally cut and inspected with a Spilker converting machine. The S-CON Starline CLS 500 is designed for cutting and inspecting printed materials at high speed. Two vacuum pull stations ensure optimum web tension during the process and enable the cutting of open adhesive and the processing of CLS® material. In contrast to cutting standard labels, which of course can also be produced on the machine, a precision micro-perforation is cut instead of a distance between the labels. Thanks to the micro-perforation for separating the labels instead of a distance significantly more labels fit on each finished roll and no matrix must be removed. In addition to the reduced amount of waste produced, it also saves resources in terms of raw material, transport and handling.
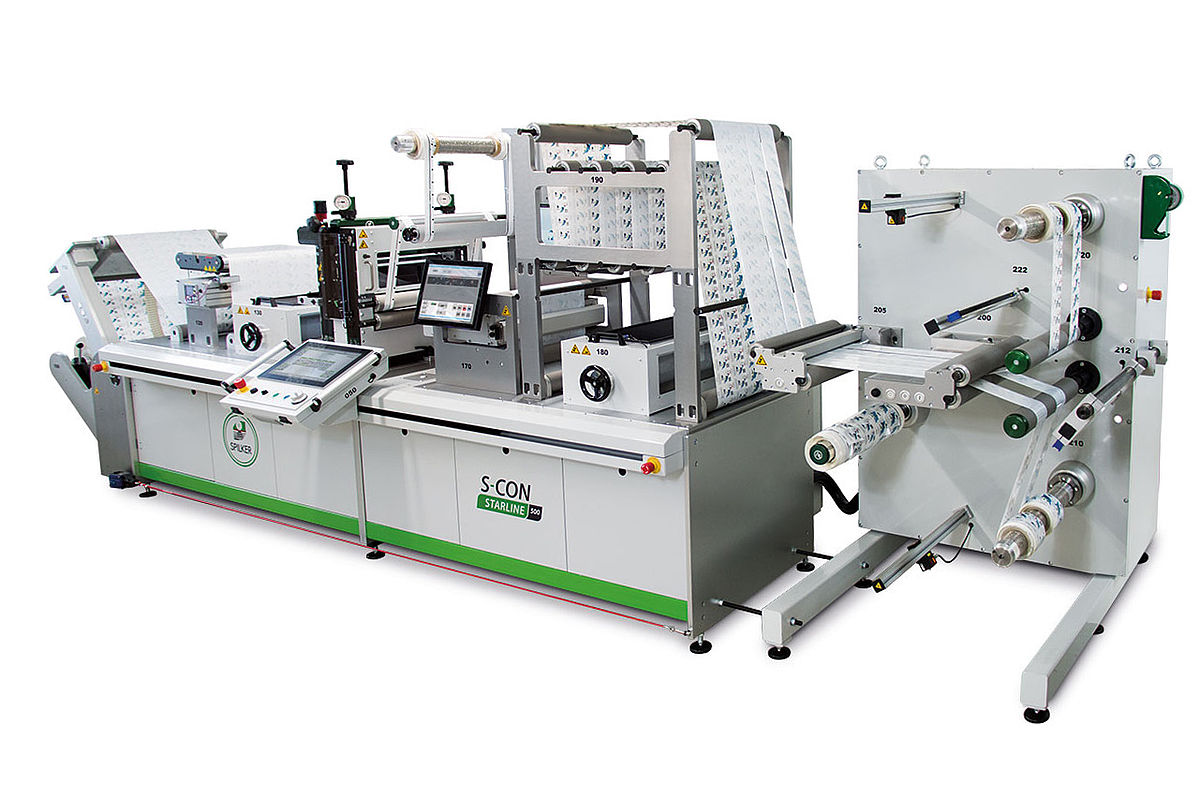
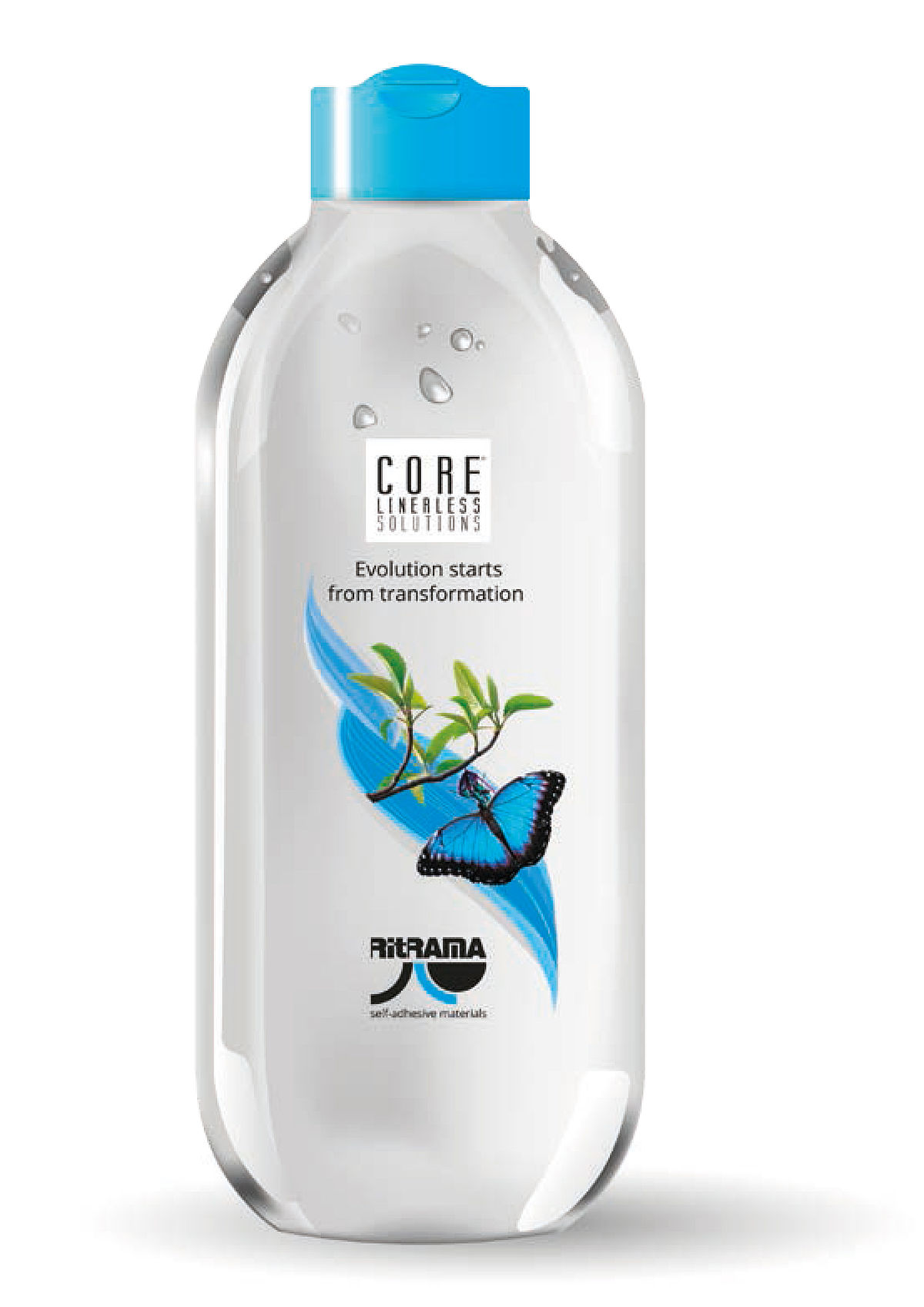
Inspection system improves product and process quality
After the cutting the perforation is controlled with a camera system to avoid problems during the later dispensing process. At the same time the printed image is checked for errors and repeat deviations, which can occur in foil materials for example during printing by material stretching, are detected and automatically compensated by the machine control. The integrated tandem winder with friction shafts finally ensures optimally wound single rolls even for narrow labels.
These finished rolls can be dispensed onto the end product using an Ilti linerless labelling machine for self-adhesive labels. The labels are separated by tearing off the micro perforation. The dispensing speed is the same as for classic labels
Environmental protection and cost reduction
The advantages of producing labels without liner are obvious: less raw material is consumed by the extremely thin material and the avoidance of the matrix. When printing, the full speed of the press can be used. Material rolls need to be changed less often because of the higher number of labels per roll, resulting in less downtime for the individual processes. Production, transport and storage costs are reduced. In addition to these economic aspects, labels produced with the CLS material contribute significantly to environmental protection since they do not generate waste.
If you also require support with a project, you can find the right contact person here:
Contact person
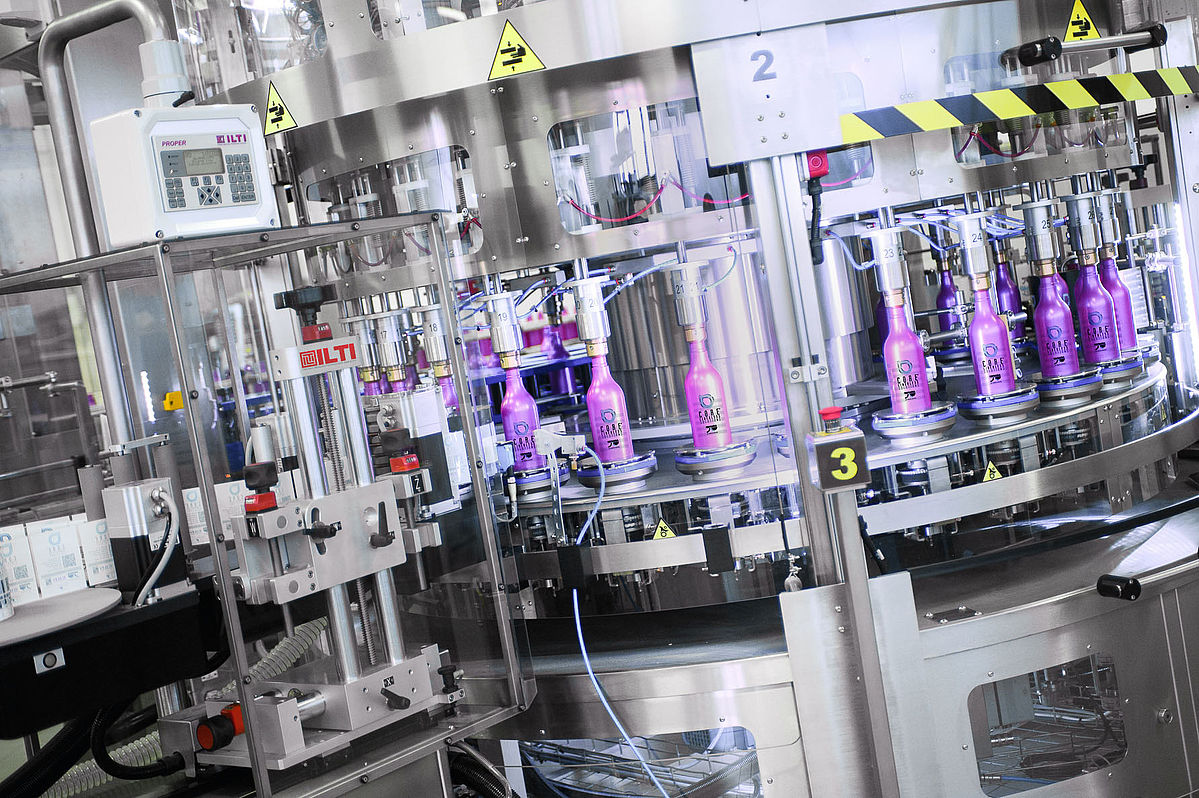